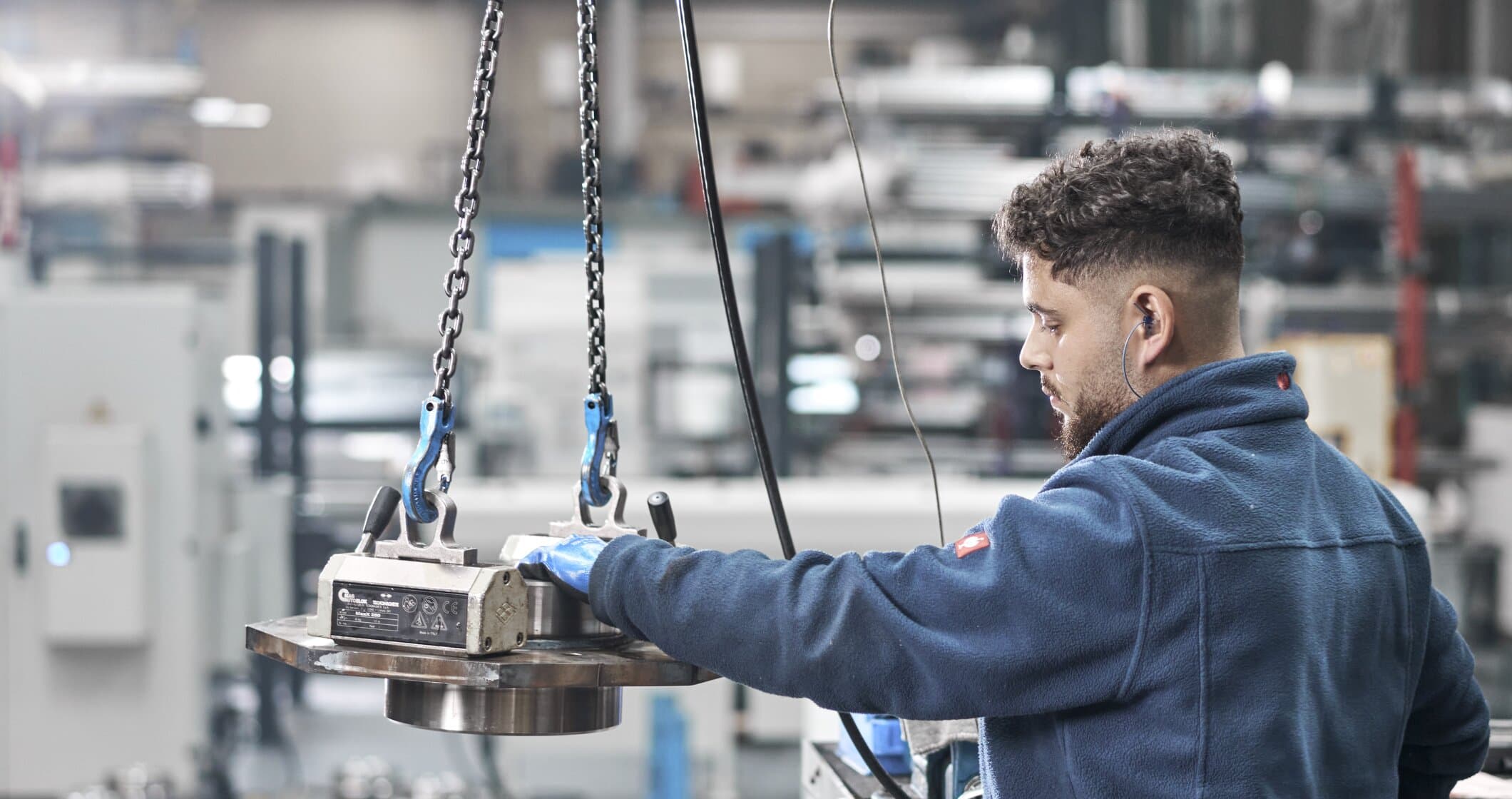
Chain wheels
Our chainwheels are manufactured from material C 45 as standard. The tooth flanks are either flame- or induction-hardened. For special application purposes are available for other steel types for manufacturing. One special quality feature of our toothed discs is the CNC contour-milled tooth contour. Together with the plane-parallel milled forks of the chain links, an optimum contact situation is guaranteed. This interaction has a positive effect on the service life of the individual components.
The best chain wheels
Depending on the application area, chainwheels need to be adapted to the respective requirement. We know which type is suitable for your industry and we will find the perfect solution. Standard is no good? Then let's develop your individual product together.
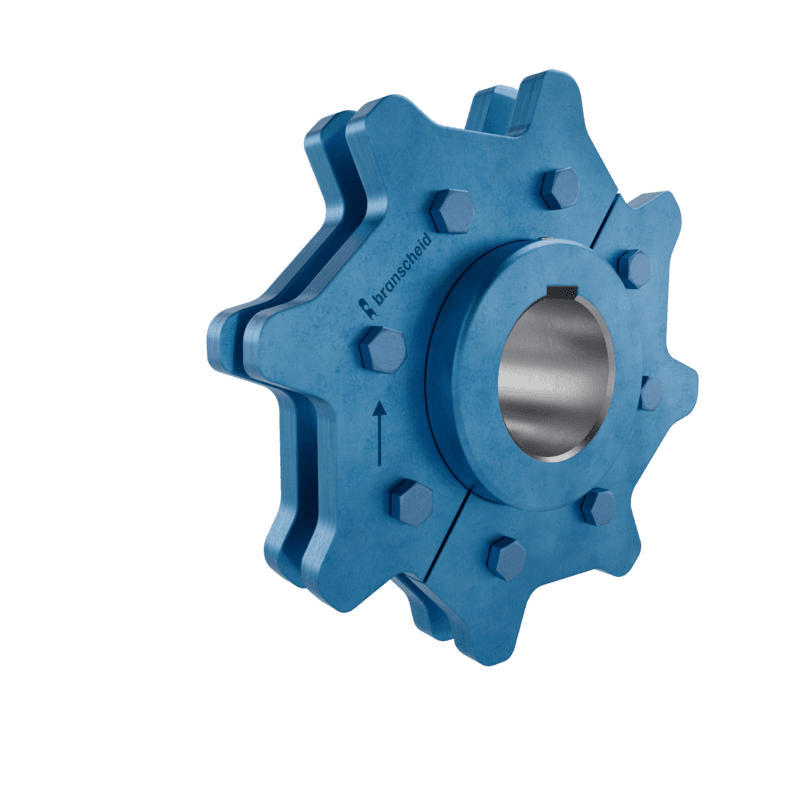
Application: this ensures optimum contact between the chain links and the bearing flanks of the chain wheels.
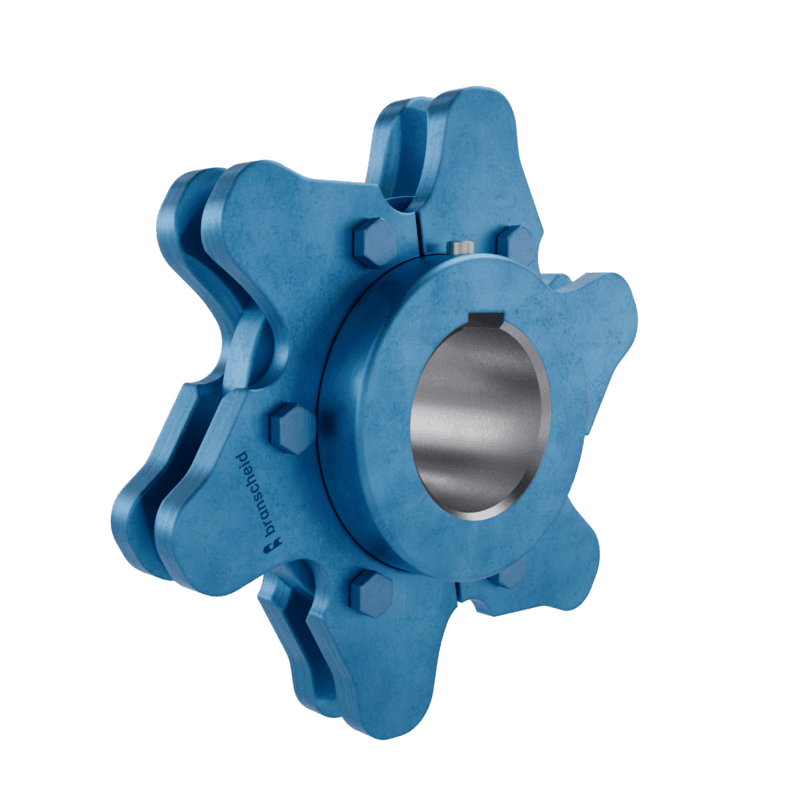
Application: for use in changing directions of rotation.
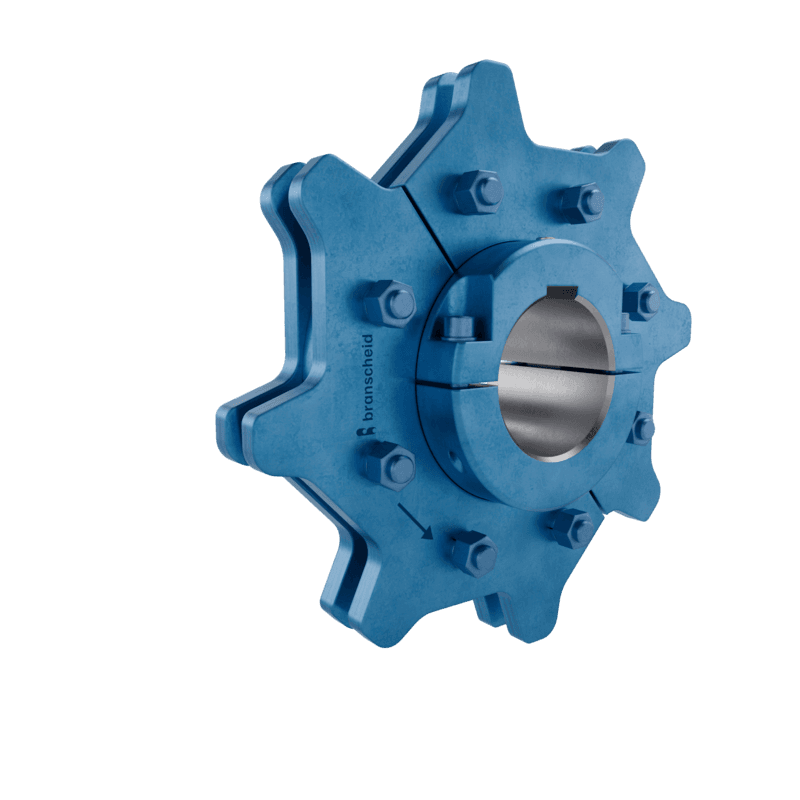
Application: divided hub for easier replacement. The shaft does not need to be removed.
Technical data & specifications
Your advantages when you choose Branscheid to be your partner
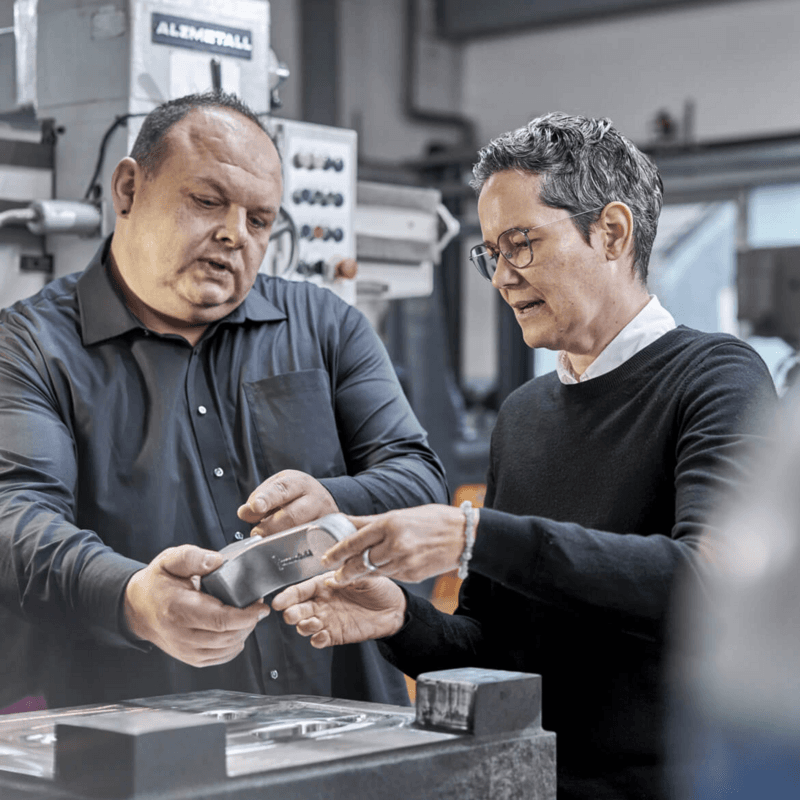
Optimum partnership
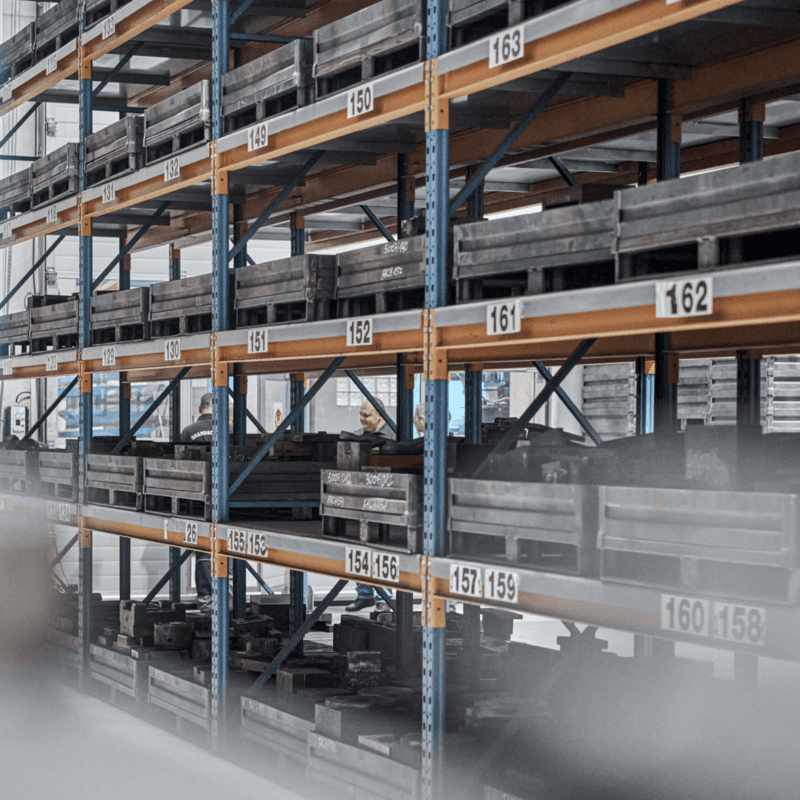
Short delivery times
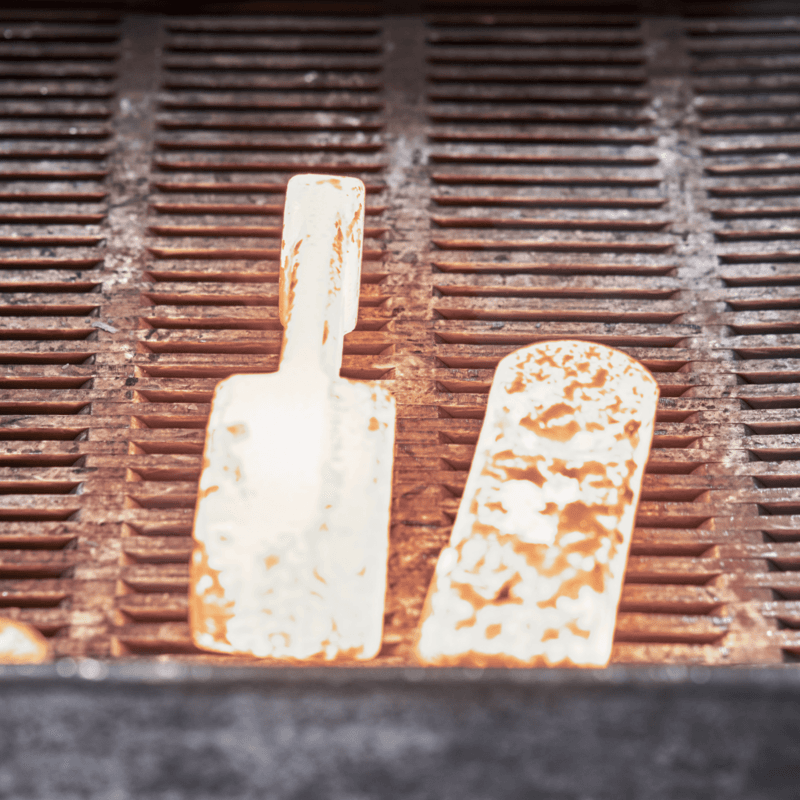
Excellent production depth
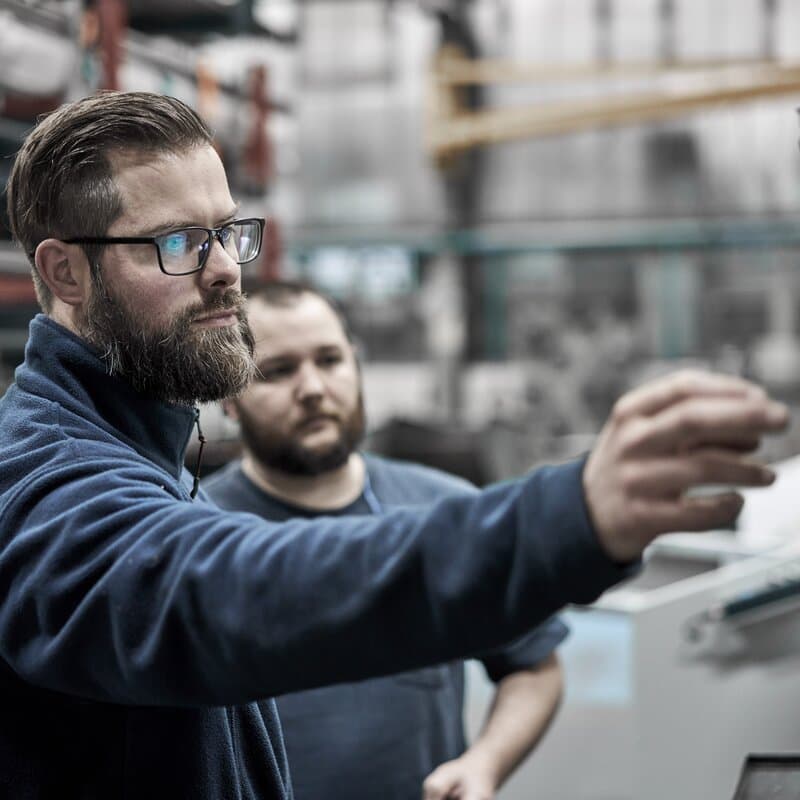
Your objectives are ours too
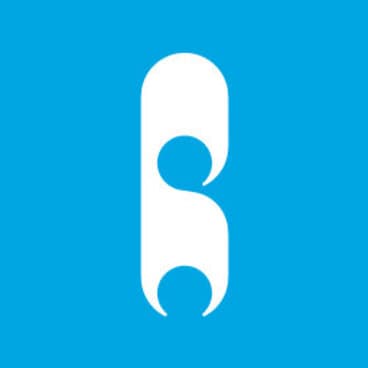
info@branscheid.com+49 2333 98 58 0